DC-53 is a general purpose cold work tool steel with exceptional Toughness, Wear Resistance, Compressive Strength and Temper Resistance. DC53, is an improvement over alloy tool steel D-2. It eliminates the disadvantages of insufficient hardness and toughness.
Smelting method : EAF+LF+VD+ESR
Main Characteristics : Relatively high tenacity, high abrasion performance, little heat treatment dimension deformation, improved coarse carbides and excellent processing performance.
Major Applications : Mainly used for precision cold pressure molds: precision punching and cutting of line cutting processing, stamping dies of various applications, etc.
Long-life automobile covered piece molds: inlaid molds of key parts.
Cut-off dies, edge rolling dies, wire drawing dies and screw dies.
Chemical constituent (%) :
C | Si | Mn | Cr | Mo |
0.93 | 0.95 | 0.40 | 7.8 | 1.90 |
W | V | P | S |
- | 0.25 | ≤0.03 | ≤0.010 |
Physical Property :
Room temperature density (kg/m³) | Specific heat of room temperature (J/Kg.K) | 200°C thermal conductivity (W/m.K) |
7.85 | 0.45 | 20.5 |
Elastic mouldsus (N/nm²) | Linear Expensivity (x10-6K) 20 ~ 200°C
20 ~ 400°C
|
218,000 |
11.9
12.3
|
Ultrasonic flaw detection :
Electric furnace steel: flaw detection standard: as per SEP1921 - D/d flaw detection or GB/T4162 Class B, or as per customer requirements.
Electroslag steel: flaw detection standard: as per SEP1921 - E/e flaw detection or GB/T4162 Class A, or as per customer requiremnts.
Purity : Electric furnace steel :
Class A | Class B | ||
Fine | Coarse | Fine | Coarse |
1.5 | 1.0 | 2.0 | 1.5 |
Class C | Class D | ||
Fine | Coarse | Fine | Coarse |
1.5 | 1.0 | 1.5 | 1.5 |
Electroslag Steel :
Class A | Class B | ||
Fine | Coarse | Fine | Coarse |
1.0 | 0.5 | 1.5 | 1.0 |
Class C | Class D | ||
Fine | Coarse | Fine | Coarse |
1.0 | 1.0 | 1.5 | 1.0 |
Delivery State :
(1) Delivery hardness: delivery under annealing state, ≤255HB;
(2) Unevenness of eutectic carbide shall comply with Bole criteria;
Supply Specification :
Round Steel | Flat Steel | Module |
Φ 1~310mm | 12~120 x 200~600mm | 120~150 x 300~600mm |
Thermal Treatment :
Softening annealing | Quenching |
Heating to 850°C for heat insulation; cooling to 650°C at 10°C C/h air cooling. | 1,030~1,050 quenching gas cooling and oil cooling (simple shape) |
Tempering |
Low temperature tempering; 180~200, tempering for twice High temperature tempering: 500~550, tempering for twice |
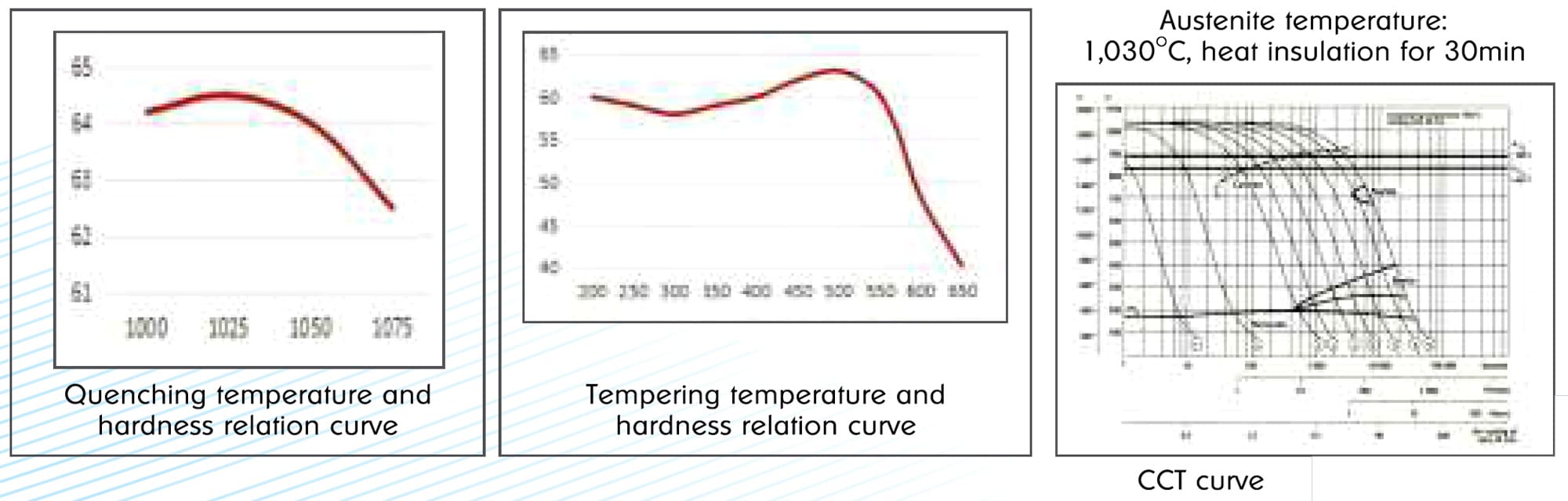